Research & Innovation
Our R&D department takes pride in its commitment to share a series of chapters available through white papers, demonstrating our determination to disseminate our knowledge and research on various topics such as the art of concrete finishing, acoustic impedance, and much more.
P2K has been doing some research in the following areas:
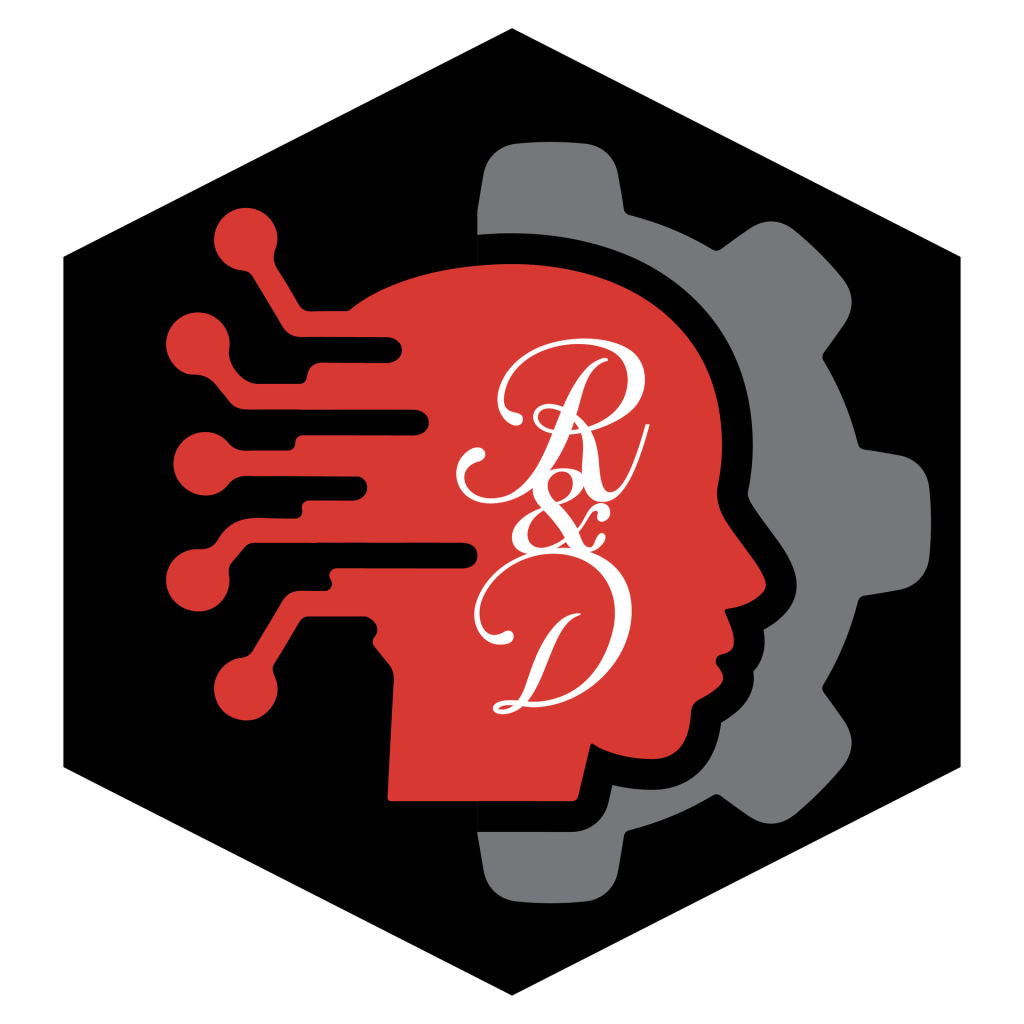
We need your feedback and help for our new products to be useful.
If you have any ideas you want to test, let us know. We will be happy to work with you.
Do you need some help?
What is R&D?
Research and development is about broadening a firm’s knowledge base and then applying this knowledge to the real world.
In 2019 Plate 2000 (P2K) began its research and development department with the aim creating a community of sharing and innovation in the concrete finishing industry. By creating this community of sharing, P2K hopes to further improve the performance of concrete finishers by providing them with the necessary tools and insight.
However, as part of the concrete finishing community, P2K needs your expertise to understand the problematic and know how we can support you in increasing your work performance even more. As part of the community, P2K is pleased to present the following series of articles (P2K Innovation Series) that will provide readers with the latest in innovation and technology in the field of concrete finishing as other fields which P2K will expand into.
Please share your thoughts with us, we would like to know your questions, your ideas and how we can work with you to develop them.
Stay tuned for our first white paper next month, P2K Innovation – The Art of Finishing, which will explain the use of different concrete finishing tools as well as the science behind concrete finishing and why it matters for professionals.
Ricardo D’Angelo, P. Eng, Ph. D
Director of Engineering & R&D Projects
The Art of Finishing
Ride-on Machine
This article, P2K Innovation – The Art of Finishing, is the first in a series of articles that will provide readers with information regarding concrete finishing tools as well as the science behind concrete finishing and why it matters for professionals.
The information provided can be used as a general reference, but can not replace the skills of the concrete finisher. Aside from the quality of equipment and tooling used, it’s the finisher who decides when finishing operations should start and troubleshoot when problems arise. The flatness and finishing of the floor are a masterful combination of the aforementioned factors.
So now, without any further ado, let’s kick this series off with a basic introduction to concrete finishing.
Let’s consider a freshly poured concrete slab which has been tooled with a screed in order to set a roughly equal height. Prior to beginning the concrete finishing using power trowels, the finisher performs the heel (footprint) test to verify the firmness of the concrete.
As a general rule of thumb finishing can begin if the depth of indentation is no deeper than 1/8”, or in some cases 1/4” and when no bleed water sheen is visible on the surface[1].
If valid, the finisher can begin finishing using power trowels (ride-ons) with float pans to treat the surface. Float pans are large metal discs (pans) that are attached to the bottom of the power trowel either by clipping onto the trowel blade or by sliding the trowel blade into a Z bracket.
Float pans permit the finisher to get onto the slab as early as possible to start finishing thanks to their large flat surface, which helps to distribute the weight of the machine evenly over a larger area. This distribution of weight allows the machine to ‘float’ on top of the concrete instead of sinking or digging in, which could happen if a machine with trowel blades is used too early in the finishing process.
The floating operation has the aim of settling the larger aggregate below the surface of a mortar composed of cement and fine aggregate from the concrete, smoothing out the surface of the wet concrete (removing slight imperfections, humps and voids), and to compact the concrete and consolidate the mortar at the surface in preparation for other finishing operations[2].
After the panning operation is performed and the concrete has partially dried, the freshly poured concrete is troweled using power trowels, fitted with either combination blades or with finish blades. Combination blades are a hybrid type flexible metal blade that are wider and more flexible than finishing blades.
The large width of the blades permits a distribution of the weight of the machine over the concrete surface during the finishing process. The large width of the blade permits a little more ‘flex’ in the blade which allows for a gradual contact between the blade surface and concrete when pitched. This property avoids the aggressive edging that would typically occur when a finishing blade is pitched at higher degrees.
Finishing blades are narrower than combination blades and are typically more rigid, which allows the finisher to apply a more aggressive edge on the blades when pitched. The troweling operation has the aim of producing a dense (compact), smooth, hard surface by successive passes made perpendicular to each previous pass. These passes also allow for the evaporation of water which may rise to the surface.
After troweling is completed a surface finish may be applied by the finisher as per the requirements of the client.
Stay tuned for our first white paper next month, P2K Innovation – The Art of Finishing Part 2, which will explain the science behind concrete finishing using walk-behind power trowels.
Ricardo D’Angelo, P. Eng, Ph. D
Director of Engineering & R&D Projects
[1] Expanded Shale, Clay & Slate Institute (ESCSI), Decembre 2003, “Finishing Lightweight Concrete Floors,” Publication #4640.
[2] American Concrete Institute, ACI 302.1R-15 – Guide to Concrete Floor and Slab Constuction. 2015. ISBN: 978-1-942727-25-5.
PART 2
The Art of Finishing
Ride-on Machine
This article, P2K Innovation – The Art of Finishing Part 2, is the second in a series of articles that will provide readers with information regarding concrete finishing tools as well as the science behind concrete finishing and why it matters for professionals. In the last article, I presented a basic introduction to concrete finishing using a ride-on as well as aim of each finishing step (floating and troweling) for the finishing process.
This article will focus on the finishing steps and tools using a walk-behind power trowel.
Concrete finishing using a walk-behind power trowel has a process similar to that of ride-on power trowels. One of the main differences is the scale of the job, with ride-ons being used for larger jobs while walk-behind for smaller jobs.
In both cases the finishing process occurs after the concrete slab is tooled with a screed in order to set a roughly equal height and after the finisher performs the heel (footprint) test to verify the firmness of the concrete[1].
Once validated, the finisher can begin finishing using the walk-behind power trowels with float pans or float blades to treat the surface. As was discussed in the previous article, float pans are large metal discs (pans) that are attached to the bottom of the power trowel either by clipping onto the trowel blade or by sliding the trowel blade into a Z bracket.
The float pans used for walk-behind power trowels are similar to those used for ride-ons except that they are smaller and have a welded block in the center which augments the handling while floating. The other method of floating is by the use of float blades. Float blades are wide flexible blades that typically clip onto the finishing blades and provide similar results to float pans.
Similar to float pans, float blades aid in distributing the weight of the machine over a larger surface area, allowing the concrete finisher to start early with the troweling process.
After the panning operation is performed and the concrete has partially dried, the freshly poured concrete is troweled using power trowels, fitted with either combination blades or with finish blades. These blades are smaller than those found on ride-on power trowels but their functionality remains the same.
For more information regarding the blades and their purposes, please check out the first article, P2K Innovation – The Art of Finishing.
Throughout the concrete finishing process, intentionally generated vibrational forces are applied to the green concrete to help it solidify and importantly, encourage the migration of water to the surface[2]. Sources of such vibrational energy include the mechanical vibrators secured to the frame of a finishing screed.
However, other inherent sources of vibration energy can also be traced to a combination of vibrations originating from the motors and rotating parts, from equipment friction, from pressures applied by the machine upon the surface and from the movement of the trowel over the surface[2]. The benefits of such vibrational energy depend both upon the nature of the vibrational energy and the state of the concrete when it is applied[2]. The amount of energy transferred from the finishing equipment to the green concrete at each stage of the finishing process depends on the applied forces of said equipment and the energy that is reflected back from the concrete to the energy source. This transmitted and reflected acoustic energy relates to acoustic impedance[2].
Acoustic impedance describes how the acoustic medium flows when exposed to the pressure of a sound wave. The acoustic impedances of an energy source and energy destination are “matched” when they are equal, thus there is no reflection of acoustic energy away from the energy destination back towards its source. The impact of the acoustic impedance on concrete can be summarized as follows, HRPO steel discs do not reproduce the acoustic impedance of concrete. This causes the internal structure of the concrete to be layered; the larger aggregates being sent to the bottom.
Other materials, such as plastics, approach the desired acoustic impedance, placing the concrete during finishing so that the internal structure is more homogeneous, limiting the stratification that currently occurs.
Plate 2000 is continually innovating and searching for new technologies that can provide you, the concrete finisher, with the pans and trowels that will best suite your demands and applications. As part of this innovation, I am pleased to share with you what is coming up in the next few weeks. Over the past months and taking into account the acoustic impedance theory, Plate 2000 has been testing and analyzing different plastics that could in the future provide you, the concrete finisher, with pans that will help you finish concrete in extreme conditions and make that finishing easier.
This week we will be testing those plastics on freshly poured concrete.
Stay tuned for our next white paper, P2K Innovation – Acoustic Impedance, which will explain in more detail the theory of acoustic impedance in concrete finishing and the impact of the power trowels machines and the materials used for float pans and trowel blades on the acoustic impedance of the concrete and its impact on the finishing process.
Ricardo D’Angelo, P. Eng, Ph. D
Director of Engineering & R&D Projects
[1] Expanded Shale, Clay & Slate Institute (ESCSI), December 2003, “Finishing Lightweight Concrete Floors,” Publication #4640.
[2] Allen Engineering Corporation Inc., 2003, Acoustic impedance matched concrete finishing, The United States Patent and Trademark Office., US6857815B2., Available at: https://patents.google.com/patent/US6857815? oq=US+6%2c857%2c815+B2, (Accessed: 09-10-2022)
The Art of Finishing
Acoustic Impedance
This article, P2K Innovation – Acoustic Impedance, is the third in the series of articles that will provide readers with information regarding concrete finishing tools as well as the science behind concrete finishing and why it matters for professionals. In the last article, I presented a basic introduction to concrete finishing using walk-behind power trowels as well as a brief introduction into acoustic impedance. This article will focus on the theory of acoustic impedance and its impact on concrete finishing.
As I mentioned in the last article, throughout the concrete finishing process, intentionally generated vibrational forces, such as those of a finishing screed, are applied to the green concrete to help it solidify and importantly, encourage the migration of water to the surface[1]. The vibrational forces put the particles of the fresh concrete in motion, reducing the friction between them and creating a temporary liquefaction of the green concrete which permits an easy settlement, placement while also reducing the number of voids within the concrete.
As a reference, the image below shows the cross section of a typical concrete carrot after the floating process is completed using a metallic pan. As one can see, there is a distribution of the coarse aggregate across the section, with no apparent voids.
An ideal concrete cross section should have a homogenized distribution of the coarse aggregate, as an accumulation or lack thereof larger aggregate in one section may contribute to the weakening and cracking of the concrete surface.
The aforementioned idealized illustration of concrete can help to explain the impact of the vibrational energy on the green concrete. However, you may be wondering how does this tie-in to the theory of acoustic impedance and the impact of acoustic impedance on the distribution of coarse aggregate in green concrete.
In the last article, I briefly defined the theory of acoustic impedance, the sources of energy and how the transfer from the energy source to the energy destination globally impacts the concrete. Now let us take a look at the how one can have a “matched” acoustic impedance between a finishing tool and the concrete on the concrete internal structure. All materials have a value of acoustic impedance and as the acoustic energy travels from the power trowel towards the concrete, it will transfer through the different interfaces, materials, and will undergo a combination of transmission (through the material) or reflection (away from it), depending on the impedance relationship. In this approximation it is assumed that there is no propagation at an angle to the interface (which would cause refraction – bending of the sound waves) and that the transfer is abrupt in nature, but the transition may be gradual. The fraction of the energy that is transmitted through the interface is linked directly to the acoustic impedances before and after the interface.
Following the conservation of energy†, the sum of the reflected energy and the transmitted energy gives the incident energy, meaning there is no loss of energy within the interface.
The notion that the transfer of energy from a concrete finishing tool to the green concrete undergoing finishing is an acoustic process, may seem confusing. However, what is important to understand is that there is a transfer of energy. As highlighted in other studies, if no transfer existed, then the impact of troweling would be null and have no impact on the concrete[1]. The same study showed that since there is a transfer of energy and since there is no significant net change in the height of the concrete after troweling, then the only possibility that remains is that troweling applies a mechanical oscillation (acoustics) to the concrete.
From the standpoint of the concrete, concrete has characteristic impedance values based on the condition of concrete, from the initial pour to it cured state. It has been noted that the values augment slowly up to the 3 hours after the initial placement and then increase linearly up to the cured state[1]. This means that the finishing trowel-pan assembly can in theory have a fixed acoustic impedance instead of a variable one.
An idealized theoretical representation of the impact of the acoustic impedance between the concrete and the energy source via a material permitting a closely matched energy and a non-matched material is shown below. The transfer of acoustic energy has been simplified to be only perpendicular to the concrete surface. (a) Illustrates the placement of the concrete mixture onto the slab. (b) The laser screed, applying vibrational energy moves the aggregate and mortar such that a flat surface is created. As in the previous figures, there is a homogenization of the concrete and a filling of the voids. (c) A HRPO steel disc is used to float the concrete, since the HRPO steel disc-trowel machine assembly is not acoustically matched, there will be a reflection of the transmitted acoustic energy from the concrete back towards the machine. The result is a layered internal structure of concrete; the larger aggregates being sent to the bottom. (d) If, however, a closely matched acoustic material is used for floating, there will be a reduction of the reflected acoustic energy; therefore, the internal structure of the concrete will be more homogenous, limiting the stratification that currently occurs.
Plate 2000 is continually innovating and searching for new technologies that can provide you, the concrete finisher, with the pans and trowels that will best suit your demands and applications. As part of this innovation, I am pleased to share with you that Plate 2000 has successfully tested two innovative pans last month on a concrete slab at our facility.
Stay tuned for our next white paper, P2K Innovation – Plastic Pans, where I will present some results from our plastic pans test using two plastics. The results will include the wear of the pans and the impact on the concrete aggregate distribution in the cross section.
Ricardo D’Angelo, P. Eng, Ph. D
Director of Engineering & R&D Projects
[1] Allen Engineering Corporation Inc., 2003, Acoustic impedance matched concrete finishing, The United States Patent and Trademark Office., US6857815B2., Available at: https://patents.google.com/patent/US6857815?oq=US+6%2c857%2c815+B2, (Accessed: 09-10-2022)
[2] Faris Matalkah, Yaser Jaradat, Parviz Soroushian. Plastic shrinkage cracking and bleeding of concrete prepared with alkali activated cement. Heliyon 5 (2019) e01514. doi: https://doi.org/10.1016/j.heliyon.2019.e01514
† Energy can neither be created nor destroyed – only converted from one form of energy to another. This means that a system always has the same amount of energy unless it’s added from the outside. For example, water is frozen by removing energy, if the same ice is heated (adding energy) it turns into water. If it is heated further (adding energy) it boils and the water becomes vapor.